There can be no doubt that latex
was used by the earliest Mesoamerican
tribes since we know that they manufactured balls from dry rubber
for the ball game and Torquemada, in “De la Monarquia Indiana”
(1615), wrote about their use of latex to waterproof fabrics used
for clothes and head coverings. He also mentioned waterproof boots
and it is well established that Amazonian natives used to make
protective shoes by using their feet as formers. After a series
of dippings in latex, with a short drying period between each,
a strong shoe could be peeled from the feet, smoked to sterilize
it and used as necessary to provide protection against rough ground
or insect bites.
A century and more later Charles
Marie de la Condamine described how natives made rubber bottles
and syringes by coating clay cores with several layers of latex,
drying between each dipping and then breaking out the core when
the required thickness was reached... The name given to the latex
gatherers even today is Seringuerio, meaning ‘maker of syringes’,
and clearly indicates the importance of this material to their
lifestyle.
At the end of the 18th century, Silvestre Diaz de la Vega, the
Director General of Tobacco in Mexico wrote extensively about
the use made of latex in that country. In 1785 his memorandum
included the observations that latex is an adhesive and can be
used on any textile. Pieces of cloth were covered with up to 10
layers of latex and the material could be used for making capes,
cloaks, boots, shoes, carriage tops all without the use of a tailor
as the seams were simply cemented together with the latex. He
himself designed and made containers to transport mercury from
Mexico to Spain. These consisted of two layers of chamois leather
bonded together with a latex film – some 20 years before
Macintosh produced his eponymous triple-layed material. In 1799
Vega wrote that “latex would become one of the most useful
products of the vegetable kingdom” he bemoaned the fact
that two centuries had passed since Hernandez described the material
and yet not a single step has been advanced in benefit of commerce,
medicine or the arts ….” The application of caoutchouc
is limited to date to a small number of contrivances which are
smeared with it to guard against humidity and a few other items
that are used in the land where it exists - all being of little
importance and less value”.
In 1791 Peal (BP1801) described the preparation of waterproof
cloth using a rubber solution in turpentine but included latex
in his patent coverage whilst Hancock,
from 1824 onwards, occasionally referred to his attempts to use
latex for a variety of applications but his attempts to obtain
regular supplies of the material were thwarted by its decomposition
and auto-coagulation. Goodyear’s one recorded use of the
material was actually by one of his assistants who dipped a pair
of trousers in latex and wore them for work when the latex had
dried. At the end of the day he was stuck to his trousers, the
trouser legs were fused together and the whole was firmly adhered
to his bench. Goodyear does not describe how he was freed but
noted that the adhesiveness of rubber must be an intrinsic property
of the material rather than a result of poor manufacturing technique.
In 1846 Parkes invented the ‘cold cure’ process whereby
rubber-coated fabrics or thin films could be vulcanized using
a solution of sulphur chloride and in 1878 Abbott patented the
use of sulphur chloride gas which avoided the problems associated
with the use, recovery and disposal of solvents.
Why then did latex technology in the west lag so far behind that
of ‘dry rubber’, particularly since the early dry
rubber technology often required that rubber to be dissolved to
give, if not latex, at least a solution which could be handled
more easily than the raw dry rubber?
The first problem to be overcome was latex
instability. The analogy to curdled milk has already been
mentioned and the causes of the two events are the same –
bacteriological attack. As early as 1791 Fourcroy had suggested
that latex could be stabilised by the addition of alkali and in
1804 he proposed (unsuccessfully) that some of this stabilised
latex should be shipped to France. In 1853 Johnson suggested ammonia
as a preservative and, indeed, supplied Hancock with some ammonia-stabilized
latex although by this time Hancock was in his 70’s and
was pretty well retired. He made no significant reported use of
it.
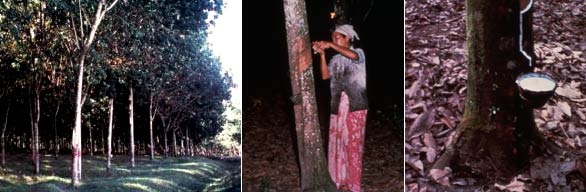 |
Modern
rubber plantation. |
Perhaps the second problem was a simple
lack of interest. The ways in which latex was collected
in the Jungles of South America or the Congo (the two largest
sources of the material) were hardly sophisticated nor were they
suited to rapid stabilization of the latex by the addition of
a chemical which was difficult to obtain in the jungles of the
two countries! Uses for solid rubber were expanding rapidly and
consumers would buy all that was on the market. It needed the
development of the rubber plantations to provide a clean bulk
supply of fresh latex which could then, if necessary, be stabilised
and shipped in that form. It should also be remembered that latex
coagulation by the addition of a weak acid such as acetic acid
was adopted by the Sri Lankan (Ceylonese) plantations around 1898
to give an extremely clean, pale golden coloured natural rubber
unlike the brown or virtually black materials available from the
wild. Like the alkali stabilization of latex, this process was
some 100 years old but, probably for the same reasons, had not
been adopted earlier. As the plantation output expanded, demand
for clean natural rubber (not latex) soared, and we arrived at
the First World War.
After the war things looked up for latex and 1920 can be taken
as the year in which its potential started to be realised.
But this brought the third problem.
Field latex, as collected, contains a lot of water. Levels vary
depending on the clone and the season but a typical composition
might be 30-40% rubber (DRC – dry rubber content), 3-5%
non-rubbers and the rest water. It was expensive to ship so much
valueless water around the world so research was directed towards
increasing the DRC of latex – now normally stabilised with
about 0.75% ammonia which was added as a gas from cylinders on
the plantation. Several methods were developed but it should be
noted that, starting from the same latex, they would yield concentrates
with different properties and applications.
Concentration methods were:
- Creaming
- Centrifuging
- Electro-decantation
- Evaporation
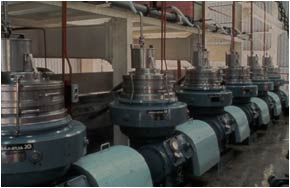 |
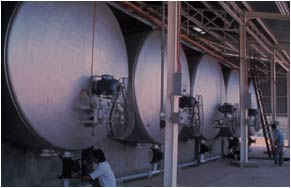 |
A
bank of centrifuges. |
Prevulcanization
tanks |
The earliest attempts to increase the DRC of latex were by creaming
– if only because it was observed to occur naturally! If
latex is allowed to stand undisturbed it, again like milk, creams,
or separates into two layers with the top one being rich in rubber
(rubber has a density slightly below that of water). Creaming
can be accelerated by warming or by the addition of certain agents
such as sodium alginate. Creamed latex typically has a DRC of
60% and a total solids content of 61.5%. It can be seen therefore
that it is proportionally much lower in non-rubbers than the initial
field latex.
Centrifugal concentration was first
used in1898 but ‘took off’ in plantations after Uttermark,
(in 1923) described in a patent how he had modified a cream separator
to produce a latex containing 60% rubber with no additives other
than the stabilising ammonia at about 0.75%. This process today
is probably the most often used.
Electro-decantation was developed
by Stamberger and Schmidt in 1937 but never seemed to be a serious
challenger to the other methods. It relied on the fact that latex
particles carry a negative charge so they will migrate towards
a positive electrode and, if the electrolysis is carried out through
a semi-permeable membrane, the concentrate will rise to the surface
where it can be creamed off. The resulting latex concentrate was
claimed to be very similar to centrifuged latex in composition
and properties.
Evaporation of the water will obviously
increase the DRC and this was the process developed by Hauser.
The process requires rather more sophistication than simple evaporation
as this will cause skin formation on the latex which will ruin
its properties. Simplistically the process begins with the addition
of a stabiliser followed by controlled evaporation off the surface
of a heated revolving drum, the bottom of which is in contact
with the latex. It is possible to obtain latex concentrates of
80% or more total solids which have the consistency of paste.
The process is reversible although the addition of water to restore
the latex has to be carried out, again, with considerable care
– hence the name of this latex (and the company which still
manufactures it – Revertex...
There was then left one final problem.
To find a method of vulcanizing
latex products that did not require the use of unpleasant chemicals
such as sulphur chloride. Although this chemical remains in use
today to make a few specific articles it has generally been abandoned
in favour of the process known as prevulcanization of the latex.
In 1921 it was discovered by Peter Schidrowitz (BP193451, 208235)
that the addition of polysulphides to latex followed by controlled
heating for a prolonged period of time gave a latex which was
visually unchanged from the starting material but, when it was
dried and gently heated, it had the properties of a normally vulcanized
piece of dry rubber. The process was known as the Vultex process.
Further work showed that by using sulphur and adding an accelerator
the process could be carried out at (tropical) ambient temperatures
and was thus ideally suited for use on rubber plantations where
the field latex could be stored in large tanks. The presence of
ammonia to preserve the latex does not interfere with the process.
The prevulcanized latex could then be converted to a product
by one of the processes described later and then gently heated
to give the finished product. The chemistry of this process was
finally understood in the 1990’s, following work at the
Malaysian Rubber Producers’ Research Association (now known
as TARRC) in the UK. It was shown using transmission electron
microscopy that there was initial crosslinking between the various
elastomer chains within each particle of latex and that, on drying
to a film, loose ends of the chains, which projected from the
surface of each particle, acted like ‘Velcro’ to hold
the particles together. Slowly at room temperature, or more rapidly
at elevated ones, the chemistry of vulcanization continued with
S-S bonds in the polysulphidic crosslinks breaking and reforming.
Some of the reformed bonds were inevitably between the entangled
polymer ends of different particles and the whole product then
became chemically ‘fused’ together.
Two particular advantages of vulcanized latex over vulcanized
‘dry’ rubber are: