To see the pictorial story of natural rubber production,
click here.
In order to utilize fully the properties of (initially)
natural rubber and (later) the synthetics, it was necessary to create
an industry that could process the raw material and make useful
products from it. While the latex industry was to be built around
a material that could be handled quite easily, dry rubber was a
very different proposition.
Raw natural rubber has a molecular weight several times greater
than most of the synthetics and in this state it is difficult
to process except as a solution (when, even then, a considerable
amount often remained as swollen gel). It is therefore necessary
to initially “break down” or masticate the material
to a dough-like consistency and it was this material which was
(eventually) used by Macintosh to give a solution of uniform viscosity
with which to manufacture his triple layer waterproof fabrics.
If the dough is not intended to be made into a solution, the
masticating process makes the addition of additives a relatively
simple procedure. The “compound”, as this material
is known, had then to be shaped and vulcanized (or cured).
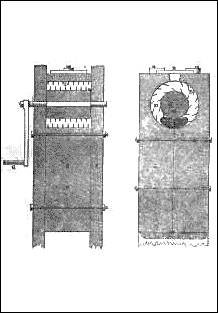 |
The mechanical processing of dry rubber began with Hancock’s
“pickling” machine (1820) which had an output
of one pound of rubber per three hours and was hand operated
( one man powered) – hardly commercial for what
was to follow - and the industrial revolution had yet
to provide an engineering industry that was equipped to
meet the demands of the rubber product manufacturers.
Indeed, it is fair to say that the two industries developed
together as demands for multi-horsepower machines built
to close tolerances grew. Incidentally, Hancock’s
“pickle” was not originally conceived to masticate
rubber but to fuse together all the little off-cuts his
various processes were producing since he had observed
that freshly cut rubber surfaces would adhere strongly
to each other, a behaviour which rapidly changed as the
edges aged.
His next machine was two-man powered but by 1821 he had
installed a horse-mill to drive several processing machines.
It was only after a fire in his London factory that, in
1834, he introduced a (steam) power driven machine into
the industry at Macintosh’s factory in Manchester.
This consisted of a single roller with a fluted surface
rotating in a concentric case. As it rotated, the rubber
was torn and so masticated as in his “pickling”
machine. This could claim to be the forerunner of today’s
internal mixer. Later models could handle up to 1800 pounds
of rubber in one charge.
|
As I have already said, a great deal of rubber was used in solution
and mastication was needed so that the rubber could dissolve without
producing too much gel, but in the 1830’s Chaffee concluded
that the use of a solvent to prepare cast thin films of rubber
was the main cause of the latter’s rapid degradation so
he developed his “calender” which consisted of 3 or
more vertically stacked rolls with adjustable “nips”
between the rollers through which the rubber dough could be passed
to produce ever thinner sheets without recourse to solvent. By
passing a sheet of fabric through the final nip together with
the rubber, rubber-impregnated material could then simply be prepared.
A year or two later he developed the
two roll, two-speed mill which rapidly replaced Hancock’s
machines. By rotating the horizontally opposed rollers in
opposite directions at slightly different speeds the rubber
could be masticated and any additives then added into the
nip so that they became finely distributed throughout the
mix. A further type of mill soon became available which
had two or more fluted rollers which could be used for washing
the crude rubber as well as pre-masticating and creping
it before passing it through the smooth-rolled mill or calender.
These machines remain the basic equipment of virtually every
rubber manufacturing facility today. |
|
Although the design and manufacture of these close-tolerance
mills and calenders seems a simple matter today, it was pushing
the frontiers of technology in the mid 19th century. Stephen Moulton
described in great detail the difficulties he, and his engineering
companies, experienced in making the rolls. The foundry was reasonably
successful in casting the hollow rolls but grinding the chilled
hollow rolls proved an exacting (and expensive) task. In 1849
Moulton wrote that he was glad that two rolls have been successfully
ground against each other “but how do you intend to grind
the third” since grinding that against one of the others
would destroy the relationship between the first two and all three
could not be ground together with the power then available in
the foundry. When Moulton complained about the cost, the foundryman
said: “if you could see the number of rolls strewing our
yard you would not complain”. Even as late as 1874 Crossley
Brothers of Manchester wrote to Moulton: “rolls never seem
worth their money. They are very risky things to make”.
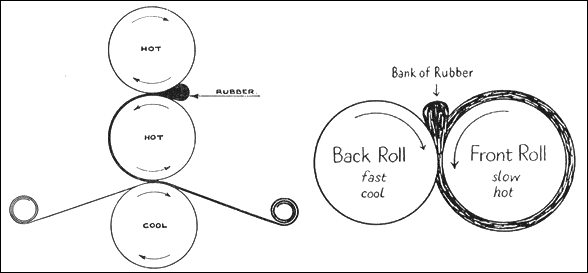
|
With the basic masticating and mixing
processes now understood, the search was on for new methods
of mixing which were quicker, less power-consuming, and
which offered a cleaner working environment than that provided
by the “open” mills. Space was always at a premium
so more compactness was added to the wish list. These requirements
led to various “internal mixers” being developed.
Werner Pfleiderer, a company that had begun some 30 years
before manufacturing machinery for mixing and kneading dough,
made the earliest in 1913 while in 1916 Fernley Banbury
launched the “Banbury” mixer which remains probably
the most popular mixer for rubber compounding in the world
today. The Banbury uses a pair of counter-rotating winged
tangential rotors inside a closed chamber into which the
rubber, and then the additives according to some pre-determined
sequence, are dropped and sealed by a ram. After mixing,
the compound is dropped through the floor of the mixer for
molding and vulcanization. Francis Shaw adopted the same
principle in the 1930’s with the “Shaw Intermix”.
|
A variation on this theme is the “intermixer” which
uses rotors which intermesh and shear/mix the rubber between the
nogs and root diameters of the rotors. Since the nogs are slewed
on the rotors the mixing material is continually swept from side
to side within the chamber to give excellent overall mixing. At
least one manufacturer today incorporates both intermixing and
tangential technology within one mixer but rubber mixing still
remains a batch process and no one has yet succeeded in devising
a fully continuous mixing process.
The next stage in the manufacture of a vulcanized rubber product
is to shape it and then apply heat to effect vulcanization. In
1855 Johnson patented the idea of using a press with shaped platens
to bring about the shaping and in 1860 Pitman introduced steam-heated
platens. This practice is still used today, although electrically
heated presses have taken an ever-increasing share of the market
in the latter third the 20th century.
As with compounding on a mill or in an internal mixer, molding
with platens is a “batch” process and this is obviously
of little use in the manufacture of articles such as hoses or
automotive rubber seals and profiles. In this area the rubber
industry learned from the plastics industry, specifically from
Bewley who had invented the plastics extruder in 1847 to extrude
gutta percha as an insulating and protective coating for the first
submarine telegraph cables.
In 1881 Francis Shaw developed the screw extruder in which the
compounded rubber was forced through an appropriately shaped die
from a large cylindrical reservoir that was compressed by a screw
piston. The product squeezed from the die (the extrudate) was
then coiled on flat pans in spirals and cured in air ovens. More
modern developments retain the extruder but use a variety of continuous
curing procedures such as salt baths or long ovens through which
the product is passed.