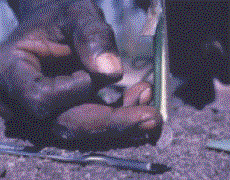 |
The plantation rubber tree is a factory, specifically
designed to produce as much latex as possible. To
this end it can be considered to consist of three
parts:
- the roots to take up sustenance
- the trunk to provide a good ‘storage and distribution
centre’
- the canopy to provide a high rate of biosynthesis.
Modern trees are often a ‘three part tree’
with these three parts grafted together from seedlings
of plants which excel in each particular area. |
|
|
|
|
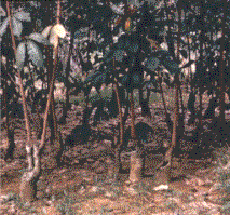 |
After
a short time growing in pots the three part trees are
planted out in a nursery before finally being transplanted
into the plantation. |
|
|
|
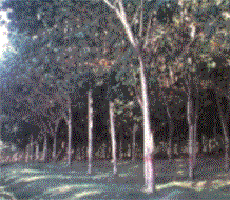 |
They
are allowed to grow for about six years and then it
becomes cost effective to tap them. |
|
|
|
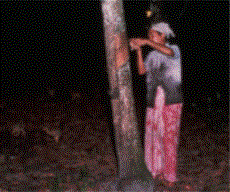 |
Tapping
is the name given to the removing of a thin sliver of
bark so that the latex can flow rather like blood from
a graze on the skin. The orange panel in the picture
opposite is the ‘tapping panel’ which slowly
moves down the tree as successive tappings are carried
out.
Tapping takes place in the early morning, before
the real heat of the day (so it is dark!).
It usually takes place every day or every other day.
|
|
|
|
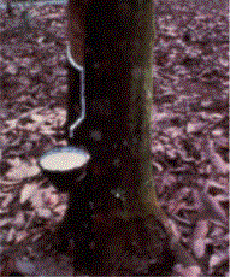 |
For
a few hours the latex flows from the ‘grazed’
trunk, runs down the gradient of the sloping panel to
a vertical cut and then to a metal spike which sticks
out of the tree and allows the latex to drip into the
collecting cup.
Eventually the flow stops as the wound heals and
the flow stops.
|
|
|
|
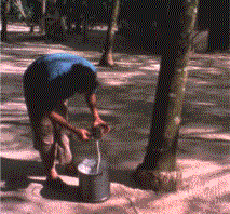 |
Later
that day the tapper goes round his/her allocated trees
to collect the latex in a pail. |
|
|
|
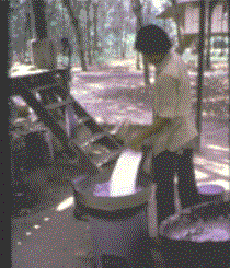 |
The pails are then filtered and bulked into drums after
which they are taken by lorry to the processing centre. |
|
|
|
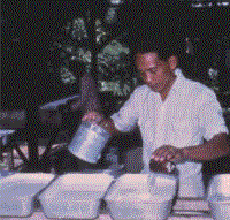 |
At
this point the latex can be treated in several ways:
The first process described is the making of ‘ribbed
smoked sheet’ (RSS) which was very popular until
the mid 1960’s but is still used to a lesser
extent today.
On a small scale, at the smallholders or a co-operative,
the latex is coagulated by the addition of a little
acid. The effect is similar to curdling milk. The
coagulum is removed.........
|
|
|
|
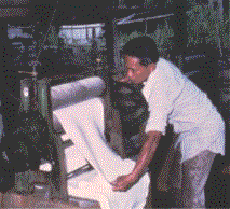 |
.........and
passed through a mill which squeezes most of the water
out of it. The rollers of the mills are patterned with
ribs which impart their imprint into the sheet hence
its name - ribbed. |
|
|
|
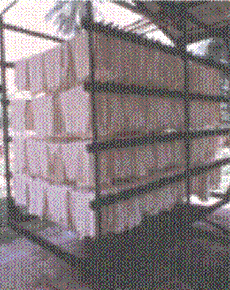 |
The
ribbed sheets are cut to size and hung out on racks
to dry before being wheeled into a smoke house where
the sheets are smoked for several hours. |
|
|
|
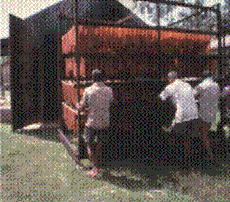 |
When
they are removed they are dry and a deep golden-brown
colour. |
|
|
|
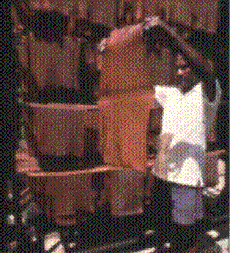 |
They
are examined by holding them up to the light and graded
on the levels of dirt seen. After which they are wrapped
together to form bales and shipped in that format. |
|
|
|
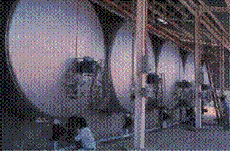 |
In another process, the latex is bulked in massive storage
tanks from which it can be run into large drums (45gal)
for sale and export or prevulcanized before being drummed
and sold. |
|
|
|
 |
The
small scale preparation of ribbed smoked sheet can be
scaled up using large tanks with baffles to separate
the coagulum......... |
|
|
|
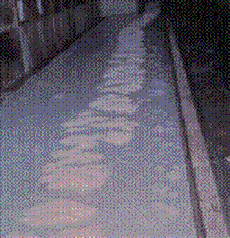 |
|
|
|
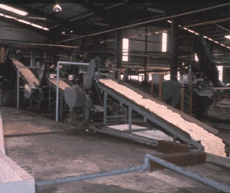 |
can
be passed through a series of rollers to give a sheet.
If a small amount of castor oil is dribbled onto
the rubber whilst it is being milled the sheet breaks
up into a crumb.........
|
|
|
|
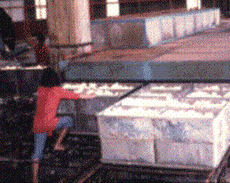 |
which
can be dried in big bins ready for weighing and bagging
as shown below. |
|
|
|
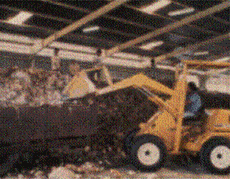 |
If
the latex is left in the collecting cup overnight it
will coagulate by itself and in any plantation there
is always scrap dry rubber to be found. This is cleaned
up and sold – mostly going into tyres. |
|
|
|
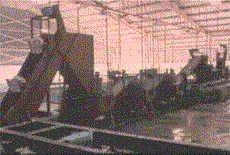 |
The
rubber is loaded onto a machine which crumbs it whilst
washing it with large quantities of water. |
|
|
|
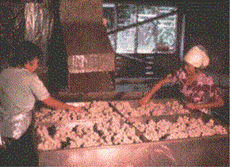 |
The
resulting crumb (much darker that that obtained from
latex is binned....... |
|
|
|
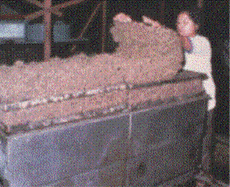 |
|
|
|
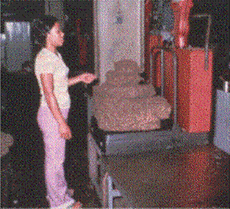 |
Weighed
to give uniformly sized bales of 25kg......... |
|
|
|
 |
|
|
|
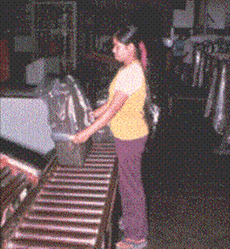 |
|
|
|
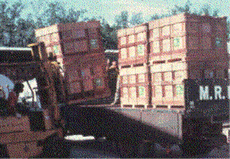 |
and
placed into 1.2 ton pallets ready for shipment.
These rubbers are graded by chemical tests, rather
than visual inspection and are sold as ‘technically
specified rubbers ‘ (TSR).
|
|